Destylacja rozpuszczalników to proces, który polega na oddzieleniu składników mieszaniny na podstawie różnicy w ich temperaturach wrzenia. W praktyce oznacza to, że gdy mieszanina jest podgrzewana, składnik o najniższej temperaturze wrzenia paruje jako pierwszy, a następnie skrapla się w chłodniejszej części aparatu destylacyjnego. Proces ten jest niezwykle istotny w chemii oraz przemyśle, ponieważ pozwala na uzyskanie czystych substancji chemicznych z różnych źródeł. Kluczowym elementem destylacji jest zastosowanie odpowiednich urządzeń, takich jak kolumny destylacyjne, które zwiększają efektywność separacji. Warto również zwrócić uwagę na to, że destylacja może być przeprowadzana w różnych warunkach ciśnienia, co wpływa na temperatury wrzenia poszczególnych składników. W przypadku destylacji próżniowej obniża się ciśnienie atmosferyczne, co pozwala na destylację substancji w niższych temperaturach, co jest szczególnie przydatne dla substancji wrażliwych na wysoką temperaturę.
Jakie są najczęściej stosowane metody destylacji rozpuszczalników
W kontekście destylacji rozpuszczalników wyróżnia się kilka metod, które różnią się między sobą zarówno techniką wykonania, jak i efektywnością separacji. Najpopularniejszą metodą jest destylacja prosta, która znajduje zastosowanie w przypadku mieszanin zawierających składniki o znacznie różniących się temperaturach wrzenia. W tym procesie ciecz jest podgrzewana do momentu osiągnięcia temperatury wrzenia najłatwiej odparowującego składnika. Kolejną powszechnie stosowaną metodą jest destylacja frakcyjna, która umożliwia separację składników o zbliżonych temperaturach wrzenia poprzez wielokrotne skraplanie i parowanie. Ta metoda wykorzystuje kolumny frakcyjne, które zwiększają powierzchnię kontaktu między parą a cieczą, co prowadzi do lepszej separacji. Istnieje także metoda destylacji azeotropowej, która polega na dodaniu substancji pomocniczej w celu zmiany właściwości mieszaniny i umożliwienia oddzielenia składników tworzących azeotrop.
Jakie są zastosowania przemysłowe destylacji rozpuszczalników
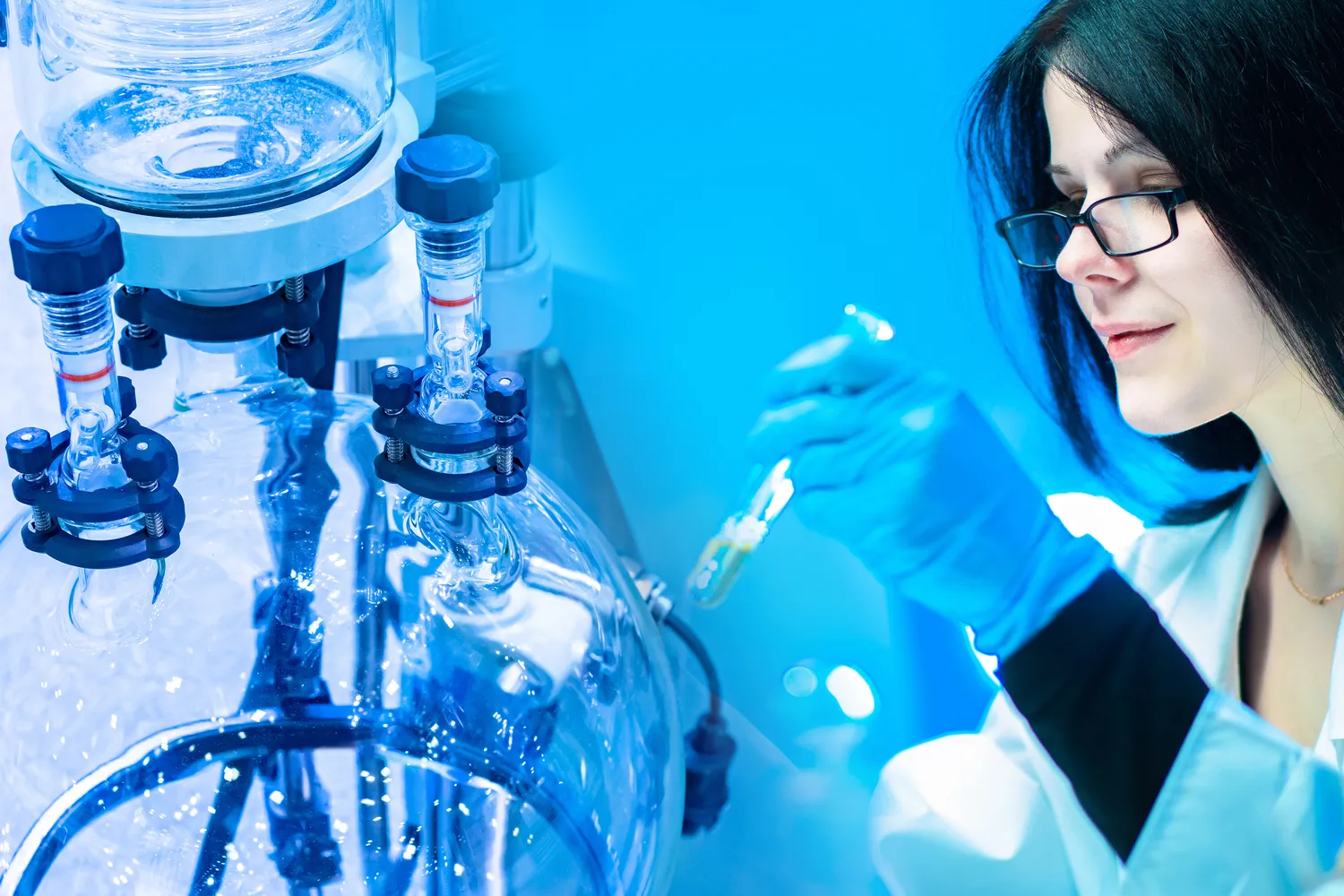
Destylacja rozpuszczalników ma szerokie zastosowanie w różnych gałęziach przemysłu, od chemicznego po farmaceutyczny. W przemyśle chemicznym proces ten jest kluczowy dla produkcji czystych substancji chemicznych, które są niezbędne do dalszych reakcji i syntez. Na przykład wiele rozpuszczalników organicznych, takich jak etanol czy aceton, uzyskuje się właśnie poprzez proces destylacji. W przemyśle petrochemicznym destylacja służy do separacji różnych frakcji ropy naftowej, co pozwala na uzyskanie paliw oraz innych produktów chemicznych. W branży farmaceutycznej natomiast proces ten jest wykorzystywany do oczyszczania substancji czynnych oraz ich prekursów przed dalszymi etapami produkcji leków. Destylacja ma także znaczenie w produkcji alkoholi wysokoprocentowych, gdzie kluczowe jest uzyskanie odpowiedniej czystości trunku. Oprócz tego proces ten znajduje zastosowanie w laboratoriach analitycznych do przygotowywania prób do badań oraz analizy jakości surowców chemicznych.
Jakie są najważniejsze czynniki wpływające na efektywność destylacji
Efektywność procesu destylacji rozpuszczalników zależy od wielu czynników, które mogą znacząco wpłynąć na wyniki końcowe. Przede wszystkim kluczową rolę odgrywa temperatura wrzenia poszczególnych składników mieszaniny; im większa różnica między nimi, tym łatwiejsza separacja. Ważnym aspektem jest także ciśnienie atmosferyczne podczas przeprowadzania procesu; obniżenie ciśnienia pozwala na obniżenie temperatury wrzenia substancji i może być korzystne dla delikatnych związków chemicznych. Kolejnym czynnikiem wpływającym na efektywność jest rodzaj użytej kolumny destylacyjnej; kolumny o większej powierzchni kontaktu między parą a cieczą umożliwiają lepszą separację składników o zbliżonych temperaturach wrzenia. Również prędkość podgrzewania ma znaczenie; zbyt szybkie podgrzewanie może prowadzić do niepełnej separacji i obniżenia jakości produktu końcowego. Ostatecznie jakość użytych materiałów wyjściowych również wpływa na efektywność procesu; zanieczyszczenia mogą komplikować proces i prowadzić do niepożądanych reakcji chemicznych.
Jakie są różnice między destylacją a innymi metodami separacji
Destylacja rozpuszczalników jest jedną z wielu metod separacji składników mieszanin, ale różni się od innych technik, takich jak ekstrakcja czy filtracja, zarówno pod względem zasady działania, jak i zastosowania. W przeciwieństwie do filtracji, która polega na oddzieleniu ciał stałych od cieczy za pomocą porowatych materiałów, destylacja opiera się na różnicy temperatur wrzenia składników. Ekstrakcja natomiast wykorzystuje różnice w rozpuszczalności substancji w różnych rozpuszczalnikach, co może być korzystne w przypadku substancji, które nie mają wyraźnych różnic w temperaturach wrzenia. Destylacja jest szczególnie przydatna w sytuacjach, gdy składniki mają zbliżone temperatury wrzenia, ponieważ pozwala na ich skuteczną separację dzięki zastosowaniu kolumn frakcyjnych. Kolejną istotną różnicą jest to, że destylacja jest procesem termicznym, który wymaga dostarczenia energii w postaci ciepła, podczas gdy inne metody mogą wykorzystywać różne mechanizmy fizyczne lub chemiczne.
Jakie są najczęstsze błędy podczas destylacji rozpuszczalników
Podczas przeprowadzania procesu destylacji rozpuszczalników istnieje wiele pułapek, które mogą prowadzić do błędów i obniżenia jakości uzyskanego produktu. Jednym z najczęstszych błędów jest niewłaściwe ustawienie temperatury podgrzewania; zbyt szybkie podgrzewanie może powodować niepełną separację składników oraz prowadzić do tzw. „przenikania” – sytuacji, w której składniki o wyższej temperaturze wrzenia również parują i trafiają do frakcji końcowej. Innym częstym problemem jest niewłaściwe dobranie kolumny destylacyjnej; kolumny o zbyt małej powierzchni kontaktu mogą nie zapewnić wystarczającej efektywności separacji. Ważne jest także monitorowanie ciśnienia atmosferycznego; zmiany ciśnienia mogą wpływać na temperatury wrzenia i prowadzić do nieprzewidywalnych rezultatów. Należy również pamiętać o czystości używanych materiałów wyjściowych; obecność zanieczyszczeń może wpłynąć na wyniki destylacji i jakość końcowego produktu. Ostatecznie brak doświadczenia operatora może prowadzić do wielu problemów; dlatego tak ważne jest odpowiednie przeszkolenie personelu oraz stosowanie się do sprawdzonych procedur operacyjnych.
Jakie są nowoczesne technologie stosowane w destylacji rozpuszczalników
W ostatnich latach nastąpił znaczny rozwój technologii związanych z procesem destylacji rozpuszczalników, co pozwoliło na zwiększenie efektywności oraz oszczędności energetycznej tego procesu. Nowoczesne systemy destylacyjne często wykorzystują automatyzację oraz zaawansowane technologie monitorowania, co umożliwia precyzyjne kontrolowanie parametrów procesu w czasie rzeczywistym. Przykładem innowacyjnej technologii jest destylacja membranowa, która wykorzystuje specjalne membrany do separacji składników na podstawie ich wielkości cząsteczek lub właściwości chemicznych. Ta metoda ma wiele zalet, takich jak mniejsze zużycie energii oraz możliwość pracy w niższych temperaturach. Innym przykładem nowoczesnej technologii jest zastosowanie nanotechnologii w budowie kolumn destylacyjnych; nanoskalowe materiały mogą zwiększać powierzchnię kontaktu między parą a cieczą, co poprawia efektywność separacji. Warto także wspomnieć o zastosowaniu sztucznej inteligencji i algorytmów uczenia maszynowego do optymalizacji procesów destylacyjnych; dzięki analizie danych można przewidywać zachowanie mieszanin oraz dostosowywać parametry procesu w celu uzyskania lepszych wyników.
Jakie są ekologiczne aspekty związane z destylacją rozpuszczalników
Ekologiczne aspekty związane z procesem destylacji rozpuszczalników stają się coraz bardziej istotne w kontekście rosnącej świadomości ekologicznej oraz regulacji dotyczących ochrony środowiska. Proces ten często wiąże się z dużym zużyciem energii, co może prowadzić do emisji gazów cieplarnianych oraz innych substancji szkodliwych dla środowiska. Dlatego ważne jest poszukiwanie alternatywnych metod separacji, które będą bardziej przyjazne dla środowiska. Przykładem może być wykorzystanie energii słonecznej lub geotermalnej do podgrzewania mieszanin zamiast tradycyjnych źródeł energii kopalnych. Ponadto wiele firm zaczyna inwestować w technologie recyklingu rozpuszczalników, co pozwala na ich ponowne wykorzystanie zamiast utylizacji jako odpadów chemicznych. Warto także zwrócić uwagę na rozwój biotechnologii i enzymatycznych metod separacji, które mogą stanowić alternatywę dla tradycyjnych procesów chemicznych. Dodatkowo wdrażanie systemów zarządzania środowiskowego w zakładach przemysłowych pozwala na monitorowanie i redukcję negatywnego wpływu produkcji na otoczenie.
Jakie są przyszłe kierunki badań nad destylacją rozpuszczalników
Przyszłe kierunki badań nad destylacją rozpuszczalników koncentrują się na poszukiwaniu innowacyjnych rozwiązań mających na celu zwiększenie efektywności tego procesu oraz minimalizację jego wpływu na środowisko. Jednym z kluczowych obszarów badań jest rozwój nowych materiałów dla kolumn destylacyjnych, które mogłyby poprawić wydajność separacji poprzez zwiększenie powierzchni kontaktu między parą a cieczą oraz optymalizację struktury wewnętrznej kolumny. Również badania nad zastosowaniem nanotechnologii mogą przynieść przełomowe rezultaty; nanoskalowe materiały mogą wykazywać unikalne właściwości fizyczne i chemiczne, które mogą być wykorzystane do poprawy procesów separacyjnych. Kolejnym interesującym kierunkiem badań jest integracja procesów destylacyjnych z innymi technologiami separacyjnymi, takimi jak ekstrakcja czy adsorpcja; takie podejście może prowadzić do stworzenia bardziej kompleksowych systemów przetwarzania chemicznego. Warto również zwrócić uwagę na badania dotyczące zastosowania sztucznej inteligencji i analizy danych w optymalizacji procesów destylacyjnych; dzięki tym technologiom możliwe będzie przewidywanie zachowań mieszanin oraz dostosowywanie parametrów procesu w czasie rzeczywistym.