Wybór odpowiedniej destylarki do rozpuszczalników jest kluczowy dla efektywności procesów chemicznych oraz bezpieczeństwa pracy. Przede wszystkim, istotne jest, aby urządzenie było wykonane z materiałów odpornych na działanie chemikaliów, co zapewnia długotrwałe użytkowanie i minimalizuje ryzyko korozji. Kolejnym ważnym aspektem jest wydajność destylacji, która powinna być dostosowana do potrzeb użytkownika. Warto zwrócić uwagę na pojemność zbiornika oraz szybkość destylacji, ponieważ te parametry mają bezpośredni wpływ na czas pracy i efektywność produkcji. Również istotne jest, aby destylarka była łatwa w obsłudze i konserwacji, co pozwala na szybkie przeprowadzanie rutynowych czynności oraz napraw. Dodatkowo, nowoczesne modele często wyposażone są w systemy automatyzacji, które zwiększają precyzję procesu oraz redukują ryzyko błędów ludzkich.
Jakie zastosowania ma destylarka do rozpuszczalników w przemyśle
Destylarka do rozpuszczalników znajduje szerokie zastosowanie w różnych gałęziach przemysłu, co czyni ją niezwykle wszechstronnym narzędziem. W przemyśle chemicznym jest wykorzystywana do oczyszczania rozpuszczalników organicznych, co pozwala na ich wielokrotne użycie i zmniejsza koszty produkcji. Dzięki temu procesowi możliwe jest uzyskanie wysokiej czystości substancji chemicznych, co jest kluczowe w wielu aplikacjach laboratoryjnych oraz przemysłowych. W branży farmaceutycznej destylarki służą do produkcji czystych substancji czynnych, które są niezbędne w procesie tworzenia leków. Dodatkowo, w przemyśle kosmetycznym destylacja pozwala na wydobycie naturalnych olejków eterycznych z roślin, które są składnikami wielu produktów pielęgnacyjnych. W sektorze spożywczym natomiast wykorzystuje się je do produkcji aromatów oraz ekstraktów smakowych.
Jakie są różnice między różnymi typami destylarek do rozpuszczalników
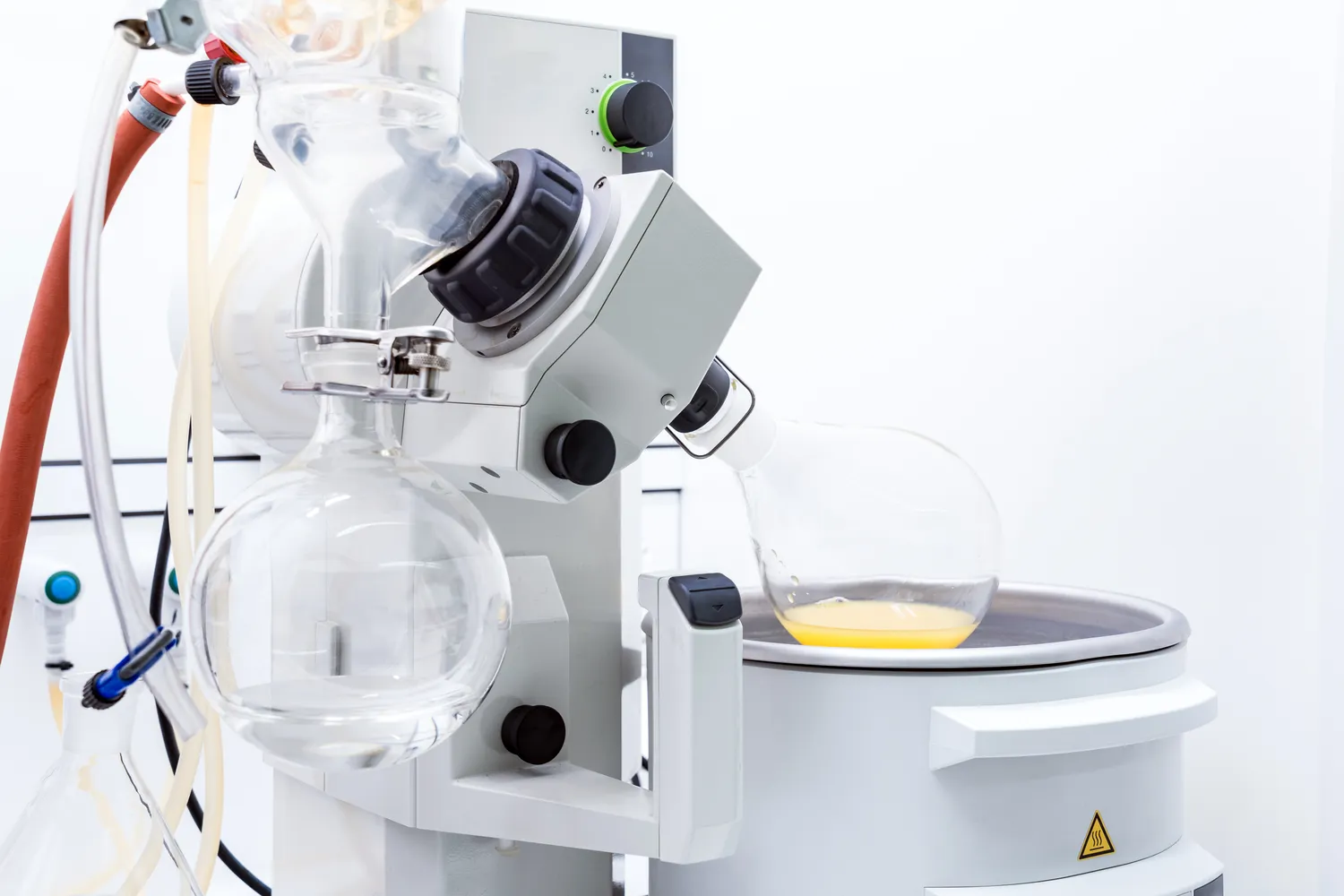
Na rynku dostępne są różne typy destylarek do rozpuszczalników, które różnią się zarówno konstrukcją, jak i przeznaczeniem. Najpopularniejsze modele to destylarki prostoliniowe oraz frakcyjne. Destylarki prostoliniowe charakteryzują się prostą budową i są idealne do podstawowych procesów destylacji, gdzie nie ma potrzeby oddzielania wielu składników jednocześnie. Z kolei destylarki frakcyjne umożliwiają bardziej skomplikowane procesy separacji dzięki zastosowaniu kolumn frakcyjnych, co pozwala na uzyskanie wyższej czystości produktów końcowych. Istnieją także destylarki rotacyjne, które działają na zasadzie obrotu zbiornika z cieczą, co przyspiesza proces odparowywania i kondensacji. Wybór odpowiedniego typu zależy od specyfiki pracy oraz wymagań dotyczących jakości końcowego produktu.
Jakie są koszty zakupu i eksploatacji destylarki do rozpuszczalników
Koszty zakupu i eksploatacji destylarki do rozpuszczalników mogą znacznie się różnić w zależności od modelu oraz producenta. Podstawowe urządzenia mogą kosztować od kilku tysięcy złotych wzwyż, podczas gdy bardziej zaawansowane modele z dodatkowymi funkcjami automatyzacji mogą osiągać ceny rzędu kilkudziesięciu tysięcy złotych. Ważnym aspektem jest również koszt eksploatacji, który obejmuje zużycie energii elektrycznej oraz konserwację urządzenia. Regularne przeglądy techniczne są niezbędne dla zapewnienia długotrwałej wydajności i bezpieczeństwa pracy. Dodatkowo warto uwzględnić koszty związane z zakupem materiałów eksploatacyjnych, takich jak uszczelki czy filtry, które mogą wymagać wymiany w trakcie użytkowania urządzenia.
Jakie są najczęstsze problemy z destylarkami do rozpuszczalników
Podczas użytkowania destylarek do rozpuszczalników mogą wystąpić różne problemy, które mogą wpływać na efektywność procesu oraz bezpieczeństwo pracy. Jednym z najczęstszych problemów jest zatykanie się rurki kondensacyjnej, co prowadzi do obniżenia wydajności destylacji. Zatykanie może być spowodowane osadami chemicznymi, które osadzają się w trakcie procesu, dlatego regularne czyszczenie i konserwacja są kluczowe dla prawidłowego funkcjonowania urządzenia. Innym istotnym problemem jest nieprawidłowe ustawienie temperatury, które może prowadzić do niepełnej destylacji lub przegrzewania substancji, co z kolei może skutkować niebezpiecznymi reakcjami chemicznymi. Warto również zwrócić uwagę na system wentylacji, ponieważ niewłaściwe odprowadzanie oparów może prowadzić do ich gromadzenia się w pomieszczeniu, co stwarza ryzyko wybuchu lub zatrucia. Dodatkowo, awarie elementów grzewczych mogą skutkować przerwami w procesie produkcji, co generuje dodatkowe koszty i opóźnienia.
Jakie są zalety korzystania z destylarki do rozpuszczalników
Korzystanie z destylarki do rozpuszczalników przynosi wiele korzyści zarówno w kontekście ekonomicznym, jak i ekologicznym. Przede wszystkim, umożliwia ona wielokrotne wykorzystanie rozpuszczalników, co znacząco obniża koszty zakupu nowych materiałów oraz zmniejsza ilość odpadów chemicznych generowanych podczas produkcji. Dzięki temu przedsiębiorstwa mogą osiągnąć lepsze wyniki finansowe oraz przyczynić się do ochrony środowiska poprzez ograniczenie emisji szkodliwych substancji. Ponadto, destylacja pozwala na uzyskanie wysokiej czystości substancji chemicznych, co jest niezwykle istotne w branżach takich jak farmaceutyka czy kosmetyki, gdzie jakość składników ma kluczowe znaczenie dla bezpieczeństwa i skuteczności produktów końcowych. Używanie destylarki zwiększa również kontrolę nad procesem produkcji, co pozwala na lepsze dostosowanie parametrów do specyficznych potrzeb danego projektu.
Jakie są podstawowe zasady bezpieczeństwa przy używaniu destylarki do rozpuszczalników
Bezpieczeństwo pracy z destylarkami do rozpuszczalników jest niezwykle istotne ze względu na potencjalne zagrożenia związane z używanymi substancjami chemicznymi. Przede wszystkim należy zawsze stosować odpowiednie środki ochrony osobistej, takie jak rękawice, okulary ochronne oraz fartuchy laboratoryjne. Ważne jest również zapewnienie odpowiedniej wentylacji w pomieszczeniu, w którym znajduje się destylarka, aby uniknąć gromadzenia się niebezpiecznych oparów. Należy także regularnie sprawdzać stan techniczny urządzenia oraz jego elementów składowych, aby zapobiec ewentualnym awariom czy wyciekom substancji chemicznych. Kolejną zasadą jest unikanie pracy z łatwopalnymi rozpuszczalnikami w pobliżu otwartego ognia lub źródeł ciepła. W przypadku wystąpienia jakichkolwiek nieprawidłowości należy natychmiast przerwać pracę i zgłosić problem odpowiednim służbom technicznym.
Jakie są różnice między destylarkami domowymi a przemysłowymi
Destylarki domowe i przemysłowe różnią się przede wszystkim pod względem konstrukcji, wydajności oraz przeznaczenia. Destylarki domowe zazwyczaj mają mniejsze pojemności i prostszą budowę, co sprawia, że są bardziej przystępne dla amatorów oraz osób zajmujących się hobbystycznym wytwarzaniem alkoholu czy olejków eterycznych. Ich koszt jest znacznie niższy niż w przypadku modeli przemysłowych, które charakteryzują się większą mocą grzewczą oraz bardziej zaawansowanymi systemami automatyzacji i kontroli procesu. Destylarki przemysłowe są projektowane z myślą o dużych ilościach surowców i wymagają bardziej skomplikowanych procesów technologicznych. Oferują one również lepszą wydajność energetyczną oraz możliwość pracy w trudnych warunkach przemysłowych. Dodatkowo modele przemysłowe często posiadają certyfikaty jakości i bezpieczeństwa, które są wymagane w wielu branżach regulowanych przez prawo.
Jakie materiały najlepiej nadają się do budowy destylarki do rozpuszczalników
Wybór odpowiednich materiałów do budowy destylarki do rozpuszczalników ma kluczowe znaczenie dla jej trwałości oraz efektywności działania. Najczęściej stosowanym materiałem jest stal nierdzewna ze względu na swoją odporność na korozję oraz wysoką temperaturę. Stal nierdzewna zapewnia również łatwość w utrzymaniu czystości i higieny, co jest szczególnie istotne w przemyśle farmaceutycznym oraz spożywczym. Inne materiały wykorzystywane w konstrukcji to szkło borokrzemowe oraz teflon, które charakteryzują się wysoką odpornością chemiczną i termiczną. Szkło borokrzemowe jest często stosowane w elementach kontaktujących się bezpośrednio z substancjami chemicznymi ze względu na swoją neutralność chemiczną oraz łatwość obserwacji procesu destylacji. Teflon natomiast znajduje zastosowanie w uszczelkach oraz elementach łączących ze względu na swoje właściwości antyadhezyjne i odporność na działanie wielu agresywnych substancji chemicznych.
Jakie są trendy w technologii destylacji rozpuszczalników
Technologia destylacji rozpuszczalników rozwija się dynamicznie wraz z postępem technologicznym oraz rosnącymi wymaganiami rynku. Obecnie coraz większą popularnością cieszą się rozwiązania oparte na automatyzacji procesów destylacyjnych, które pozwalają na zwiększenie precyzji oraz efektywności produkcji. Nowoczesne systemy monitorowania umożliwiają bieżące śledzenie parametrów pracy urządzenia oraz szybką reakcję na ewentualne nieprawidłowości. Wprowadzenie technologii IoT (Internet of Things) pozwala na zdalne zarządzanie procesem destylacji oraz integrację urządzeń z innymi systemami produkcyjnymi. Dodatkowo rośnie zainteresowanie ekologicznymi rozwiązaniami, takimi jak odzysk energii czy minimalizacja odpadów chemicznych poprzez recykling rozpuszczalników. Wiele firm inwestuje również w badania nad nowymi metodami separacji substancji chemicznych, które mogą być bardziej efektywne niż tradycyjna destylacja.